Фабрики эффективности
На Среднем Урале работает универсальная площадка для моделирования любых рабочих процессов
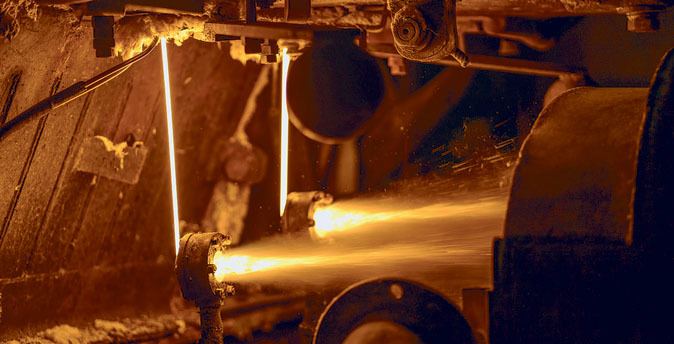
Площадка практического обучения Свердловского РЦК помогает эффективно освоить бережливое производство и справиться с сопротивлением сотрудников
В 2018 году Свердловская область стала одним из пилотных регионов для национального проекта «Производительность труда». С тех пор в него включились 220 местных компаний. Суммарный экономический эффект от роста производительности труда свердловских предприятий-участников нацпроекта превысил 3 млрд рублей.
Первым шагом к росту эффективности более 1700 сотрудников и руководителей предприятий-участников стало участие в одной из первых в России «Фабрике процессов», которая открылась в Екатеринбурге.
Суть этой учебно-производственной площадки — в создании типичного производственного или офисного процесса, который содержит множество «неэффективностей». Сотрудники и руководители учатся находить и устранять их с помощью инструментов бережливого производства. Полученные навыки они затем применяют в своей компании: устраняют потери, снижают издержки, повышают производительность труда. Для предприятий — участников нацпроекта такие тренинги бесплатны. На коммерческой основе в них могут участвовать все компании.
Свердловская площадка функционирует на базе Регионального центра компетенций в сфере производительности труда (РЦК) — местного оператора национального проекта. Она работает на основе тех же инструментов бережливого производства, которые используют для повышения производительности предприятий, и того опыта, который аккумулируют во время этой работы эксперты Центра.
— Мы хотели создать универсальную площадку, которая подходит для моделирования любых рабочих процессов, — рассказывает руководитель проектов РЦК Салават Ахмадиев.
Цех на трех столах
Первым учебно-практическим модулем «Фабрики процессов» стала оптимизация производственных процессов. Затем к ней добавился «офисный» модуль, до конца 2023 года откроется третье направление — «Логистика и склад».
Каждый тренинг длится восемь часов и состоит из серии лекций, деловых игр и практических сессий, где руководители и сотрудники компаний учатся выстраивать работу по принципам бережливого производства: находить потери и «окна возможностей», оптимизировать логистику и ресурсы, сокращать производственные площади, балансировать загрузку операторов, выстраивать работу подразделений в одном ритме.
— Эффективное производство нельзя построить за один день. Это процесс постоянного совершенствования операций и взаимодействия. Наши эксперты по полгода работают в компании: изучают принципы организации процессов, ищут проблемы, помогают оптимизировать пилотный производственный участок (поток). Но дня достаточно, чтобы наглядно показать, насколько инструменты бережливого производства эффективны и универсальны. Люди начинают замечать трудности, которые мешают работать продуктивнее, и резервы производительности, о которых не подозревали, а затем примеряют увиденное на свои реальные рабочие места, — отмечает Александр Казаков, генеральный директор областного Фонда технологического развития промышленности, на базе которого работает свердловский РЦК.
Теорию отрабатывают во время трех «смен» по 20 минут. Для этого тренеры создают предприятие в миниатюре, где участники решают конкретные производственные задачи. В каждой «компании» есть свои сотрудники, рабочие процессы, логистические маршруты и проблемы. Главная задача участников — научиться находить и решать их.
— Можно долго объяснять, что такое lean-производство и насколько оно выгодно для компании: читать лекции, рассказывать о нормах научной организации труда в СССР, о японской системе бережливого производства, которая родилась в середине прошлого века в «Тойоте».Но быстрее и эффективнее не рассказывать, а показывать. Еще лучше — дать людям самим опробовать, в прямом смысле слова пощупать руками эту систему, — объясняет логику работы «Фабрики процессов» Александр Казаков.
Благодаря небольшому размеру и простоте восприятия на таком «производстве» сразу становятся заметны все логистические и производственные проблемы, несогласованности между процессами и отделами, места, которые, словно бутылочные горлышки, тормозят движение документов или заготовок.
Юрист на час
Другое достоинство «фабричной» модели в том, что она позволяет быстро проверить любые, даже самые нестандартные решения по оптимизации работы офиса или производства. Тут же можно оценить результат этих решений, в том числе экономический. При этом нет риска подвести клиентов, если «провалиться» в качестве или сорвать сроки.
Во время тренингов сотрудники обмениваются обязанностями и пробуют себя в новой роли: бухгалтер становится юристом, а начальник цеха — рядовым сборщиком и наоборот. Это помогает лучше понять специфику смежных отделов, наладить с ними взаимодействие, а порой и найти неожиданные решения.
При отлаженной вертикальной (административной) иерархии горизонтальные связи (между обрабатывающими центрами или подразделениями) часто не отличаются эффективностью. Люди живут своим участком работы, не задумываясь о том, как он влияет на качество или эффективность конечного продукта или услуги. На «Фабрике процессов» участники начинают мыслить шире и понимать свой вклад в процесс и в конечный результат деятельности компании. Человек чувствует себя важной частью целого. Как результат, по всей цепочке создания ценности появляются рационализаторские предложения.
— Тренинг оказался очень полезным. И для предприятия, и для меня лично — в первую очередь потому, что коллеги увидели, как работают и чем живут «снабженцы». Когда примерили на себя эту роль, они удивились, как много рутинной, сложной и важной работы выполняет это подразделение, — рассказывает Виктор Колтунов, директор по закупкам Уральского завода химического машиностроения.
В 2023 году «Уралхиммаш» включился в нацпроект «Производительность труда». Оценив эффективность инструментов бережливого производства, руководство продолжило сотрудничество с РЦК на коммерческой основе и направило сотрудников на новое обучение — на «Фабрику офисных процессов».
Зона неэффективного комфорта
У «Фабрики процессов» есть еще одна задача - изменить негативное отношение персонала к бережливому производству. Как показала практика, попытки приглашенных экспертов поднять эффективность труда сотрудники часто воспринимают как попытку заставить их работать усерднее. Экспертам приходится объяснять: если найти и убрать потери, люди будут делать и зарабатывать больше за то же время. Часто им придется тратить меньше сил, а работать станет удобнее.
— «Чему вы можете нас научить», «мы лучше знаем свою работу», «десять лет так работаем и все получается» - такие фразы мы слышим очень часто. Кто-то искренне не понимает, чем мы можем помочь, а кто-то просто не хочет менять удобные привычки, — рассказывает тренер РЦК Максим Бунаков.
— Мы столкнулись с сопротивлением некоторых линейных мастеров и рабочих. Особо тяжело изменения восприняли «старожилы». Наша психика устроена так, что люди неохотно выходят из зоны комфорта и стараются избегать дополнительной нагрузки, —говорит Александр Соколов, заместитель директора по производству - начальник огнеупорного производства Сухоложского огнеупорного завода:
— Когда мы внедряли стандарты бережливого производства, многие встретили изменения в штыки. Даже если в разговоре люди соглашались, что лучше делать так-то и так-то - часто все оставалось на словах. Для этого всегда находилась куча причин и отговорок, — вспоминает Максим Суслов, директор по развитию концерна «Уралэлектроремонт».
Амбассадоры бережливости
Повысить лояльность персонала можно, если идеи бережливого производства будут нести не «пришлые» эксперты, а собственные сотрудники и топ-менеджеры — например, те, кто убедился в их результативности на «Фабрике процессов».
- К «своим» всегда относятся лояльнее. На одном из предприятий меня в открытую спрашивали – «А зачем нам это надо?». Но когда работать с «сопротивленцами» начали внутренние тренеры, дело пошло. Те, кто больше всех возмущался и противился изменениям, первыми внедрили lean-инструменты, - вспоминает руководитель проектов РЦК Наргиз Гасанова.
Эксперты Центра рассказывают: на тренингах люди видят, насколько быстрее и эффективнее идет работа, если убрать проблемы, которые не видно «замыленным» взглядом. Из скрытых противников lean-системы или «сомневающихся» сотрудники превращаются в союзников и «амбассадоров» бережливого производства, которые помогают внедрить в компании lean-инструменты.
«Участие в тренингах помогает сотрудникам понять, зачем компания решила меняться и внедряет бережливое производство, какими будут результаты этой перестройки. Люди убеждаются: эксперт следит за ними с секундомером, не чтобы выставить их тунеядцами и заставить «больше пахать». У него другая задача - понять, из каких этапов состоит производство, чтобы сделать его проще, быстрее и эффективнее». Максим Бунаков, тренер «Фабрики процессов» РЦК Свердловской области.
На тренинге люди изменились. У них поменялось мировоззрение, появились критический взгляд на работу и мотивация что-то менять, а не слепо следовать привычному шаблону. Как результат, выросло число рацпредложений, — рассказывает Александр Пономарев, руководитель отдела отраслевых продаж Уральского завода эластомерных уплотнений.
Подобный результат отмечает и другой участник тренинга — бригадир монтажников НПО «Спектрон» Олег Калиниченко:
— Я теперь постоянно прокручиваю в голове: а если сделать так или вот так — как это будет работать? А можно ли сделать лучше? И так — на каждом этапе производства. Эта привычка появилась после «Фабрики процессов» — и оказалась весьма полезной в работе.
Фабрика промышленных «звезд»
Посмотреть на работу «Фабрики процессов» вживую можно будет на III Кубке по рационализации и производительности с 13 по 17 ноября. В МВЦ «Екатеринбург-Экспо» встретятся больше 500 конкурсантов и экспертов конкурса. Команды предприятий-участников нацпроекта «Производительность труда» и государственных корпораций, студенты вузов и колледжей, будут соревноваться по 12 направлениям — от теории решения изобретательских задач и внедрения лазерных технологий до оптимизации работы бройлерного производства и обслуживания межрельсовых скреплений на железной дороге.
Одним из треков Кубка станет «Фабрика производственных процессов». Участникам нужно будет выстроить работу компании, которая сможет с минимальной себестоимостью и максимальной прибылью выпускать изделия нужного качества — пульты управления регулятора давления газа.
Создать свое бережливое производство и завоевать кубок попытаются девять команд из семи регионов, в том числе две свердловские. Это коллективы завода «Вентпром», который во всероссийском отборочном туре занял шестое место, и Сухоложского огнеупорного завода, ставшего третьим.
Перед началом конкурса обе команды прошли обучение на «Фабрике процессов» свердловского РЦК. Для них подготовили модифицированную версию тренинга, чтобы оценить, насколько гибко сможет работать команда и как быстро реагировать на запросы клиента.
На обоих предприятиях не исключают, что после конкурса снова направят сотрудников на обучение. По словам тренеров РЦК, площадка готова их принять: как с улыбкой говорят эксперты, их «фабрика промышленных «звезд» открыта всегда.
Автор Кирилл Кирягин
Свердловская параСвердловские участники предстоящего III Кубка по рационализации и производительности — коллективы завода «Вентпром», который во всероссийском отборочном туре занял шестое место, и Сухоложского огнеупорного завода, ставшего третьим. Оба предприятия — участники национального проекта «Производительность труда». «Вентпром» — градообразующее предприятие Артемовска и единственный в России производитель вентиляторов главного проветривания для шахт, тоннелей и метрополитенов — в рамках нацпроекта оптимизировал изготовление роторов. Компания за полгода ускорила выпуск изделий на пилотном участке на 77%, уменьшила долю НЗП на 33% и подняла выработку на 28%. Сухоложский завод — одно из ведущих отечественных предприятий по производству алюмосиликатных огнеупоров и высокотемпературной теплоизоляции — сегодня оптимизирует выпуск огнеупорных изделий полусухим способом. С помощью экспертов РЦК завод поднял выработку на пилотном участке с 11,7 до 14,1 тонны на сотрудника в смену, снизил незавершенное производство с 68 до 50 тонн и сократил время выпуска продукции с 216 до 190 часов. |