На автозаводе «УРАЛ» внедрили отечественную цифровую платформу для управления производством
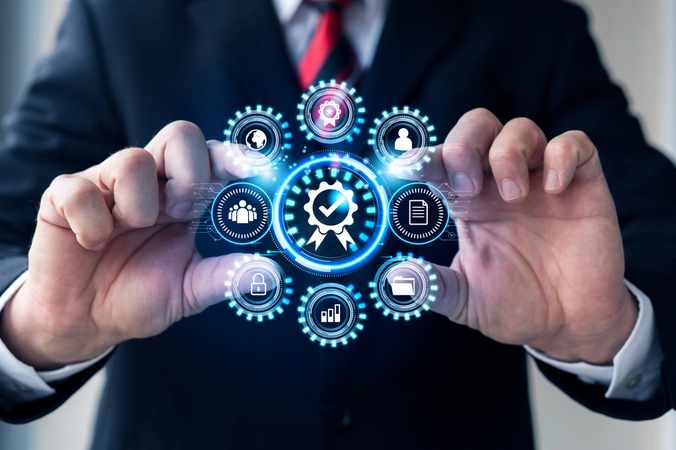
Это первый в стране проект на платформе 1С по внедрению системы оперативного управления сборочным производством для предприятия, выпускающего тяжелые грузовые автомобили
В 2020 году был дан старт проекта по цифровой трансформации АЗ «УРАЛ», в связи с геополитической обстановкой завод принял решение отказаться от зарубежной информационной системы, частично выполняющей функции по управлению производством, и перейти на российское ПО, сообщили в пресс-службе автозавода.
Для цифровизации производства был выбран системный интегратор PROF-IT GROUP с опытом реализации подобных проектов на платформе 1C:Предприятие в автомобильной промышленности. Основой для построения новой информационной системы управления производством стало решение PROF-IT MES на платформе 1С:Предприятие, созданное PROF-IT GROUP на основе лучшего российского и зарубежного отраслевого опыта.
В рамках проекта были внедрены функциональные блоки MES и QMS. Блок MES гарантирует прослеживаемость производства, позволяет синхронизировать работы служб по всему технологическому циклу, осуществляет автоматическую выдачу заданий на подсборки по вытягивающему методу, поддерживает выполнение техпроцесса, автоматизированный контроль исполнения ключевых операций и онлайн-контроль работы конвейера с визуализацией и оповещением по заданным параметрам и условиям.
Из основных особенностей внедрения блока MES можно отметить обеспечение функции контроля производства каждого автомобиля и его основных компонентов в режиме, близком к режиму реального времени. MES позволяет оперативно реагировать на различные ситуации, возникающие в ходе производства сложной техники по всей цепочке изготовления, начиная от рам и мостов и заканчивая полностью готовым автомобилем с учетом его модификации и комплектации.
Блок QMS предоставляет достоверную информацию по уровню качества продукции в режиме онлайн, блокирует продукцию несоответствующего качества, регистрирует критичные и системные дефекты, осуществляет автоматический сбор данных с диагностических устройств и стендов и обеспечивает непрерывный контроль качества выпускаемой продукции, включая процесс аудита готового продукта.
Блок QMS интегрирован с MES в части регистрации прохождения контрольных точек заказов и связанной с этим логикой управления производственным процессом. В подавляющем случае все рабочие места контролеров ОТК оснащены мобильными планшетами.
В рамках реализации проекта настроены рабочие места на сборочных конвейерах, на участках сварки, окраски, подсборки основных узлов и производства автокомпонентов, включая изготовление рам, мостов, редукторов, платформы и тележки подвески. Обеспечена диспетчеризация работы главного сборочного конвейера, окраски, производства рам, мостов и сварки кабин на всех основных потоках и конвейерах, связанная с этим интеграция данных MES с ERP-системой предприятия. Оцифрованы процессы качества по регистрации дефектов, выполнению проверок, аудитов и получения отчетности, планирования мероприятий по качеству.
С помощью MES-системы удалось выстроить сквозное управление производством не только на этапе сборки автомобилей, но и во время сборки ключевых компонентов. Полностью реализована идея прослеживаемости компонентов до установки на автомобиль - с сохранением истории по качеству каждого изделия. Для достижения наибольшей эффективности MES и QMS интегрированы с основными системами, обеспечивающими поддержку процессов управления и обеспечения производства: 1С:ERP и WMS.
«В результате проекта создана единая независимая инфраструктура, снижена стоимость владения ПО за счет сокращения количества используемых платформ, снижено время на согласование конструкторского изменения. Очень важно, что мы используем только отечественное ПО. Внедрение PLM, ERP и MES позволяют нам идти дальше в «цех», продолжая и совершенствуя цифровизацию завода», – отметил Эльдар Гумурзаков, начальник управления информационных технологий АЗ «УРАЛ».
«Задача нашей проектной команды – создать основу для эффективной деятельности всех служб и отделов завода: производства, фронт- и бэк-офиса. Это шаг для построения прозрачного цифрового производства. Благодаря прослеживаемости завод получил возможность не только контролировать качество продукции, своевременно устраняя ошибки производства, но и вести статистику качества компонентов и эффективности производства. Мы как интегратор всегда готовы поддерживать цифровизацию российских предприятий в отрасли машиностроения, и рады оказанному доверию со стороны АЗ «УРАЛ», – отметил Евгений Сударкин, генеральный директор PROF-IT GROUP.
В дальнейшем планируется функциональное расширение и развитие проекта на базе внедренной платформы: создание системы ANDON, интеграция с умным инструментом и диагностическими стендами, тиражирование созданного решения на новые производства. Продолжаются работы по автоматизации контроля качества на производстве. Рассматривается вопрос внедрения глобальной системы по управлению качеством на всем жизненном цикле выпускаемой продукции QMS Professional.